As the “power heart” of modern industry, the performance of centrifugal air compressors is directly tied to productivity, energy efficiency, and equipment longevity. However, lurking within the system is a potentially catastrophic issue—surge.
Surge not only leads to severe vibration and damage to bearings but, in extreme cases, can even result in explosion hazards. In fact, industry statistics show that up to 35% of summer compressor failures are linked to surge, and energy costs can rise by 20%–30% due to inefficient operation.
This article provides a comprehensive anti-surge guide, combining technical principles and field-proven practices to help you safeguard your equipment.
🌪 What Is Surge in Centrifugal Compressors?
1. Understanding the Surge Phenomenon
Surge is a rapid, oscillating flow reversal that occurs when the compressor operates under low flow conditions, especially near or below the surge line (Qjmin). Common symptoms include:
-
Abnormal noise: A wheezing, popping sound similar to asthma breathing.
-
Severe pressure fluctuations: The outlet pressure and flow vary wildly; gauge needles swing erratically.
-
Mechanical damage: Vibration levels can exceed 80 μm, accelerating wear on bearings, seals, and rotor components.
2. Root Causes of Surge
There are three primary reasons surge occurs in centrifugal compressors:
-
Insufficient inlet flow: Operating below Qjmin causes flow separation and backflow in the impeller.
-
System resistance increase: Closing the outlet valve or a clogged pipeline raises backpressure, pushing the compressor into the surge region.
-
Degradation of equipment performance: Impeller wear or fouled diffusers shift the compressor curve leftward, reducing surge margin.

🛡 4 Core Anti-Surge Strategies
Preventing surge is about predicting, preventing, and protecting at every stage of operation. Here’s how:
1. Flow Control – The First Line of Defense
-
Bypass Recirculation System: Install an anti-surge valve at the discharge. When flow nears surge conditions, part of the air is cooled and routed back to the inlet, maintaining minimum flow.
-
Inlet Guide Vane Adjustment: Fine-tune intake flow by adjusting guide vanes. Ensure actuator response time ≤ 0.5 seconds for rapid stabilization.
-
Stable Operating Range Expansion: A well-tuned guide vane system increases the stable operating envelope, delaying the surge onset.
2. Mechanical Maintenance – Prevent Internal Failures
-
Quarterly Inspection of Key Components:
-
Impeller: Use a borescope to check blade wear. If erosion > 2 mm, repair immediately.
-
Diffuser: Replace when corrosion rate exceeds 0.5 mm/year.
-
-
Rotor Balancing: Perform dynamic balancing to G2.5 accuracy annually to suppress vibration-induced surges.
-
Filter Monitoring: Replace air filters when pressure drop exceeds 10 kPa to prevent inlet obstruction and flow drop.
3. Smart Control Systems – From Reactive to Predictive
-
Dynamic Surge Curve Updates: Every 3 years, recalibrate the surge line using real-world data to account for performance drift due to wear or gas property changes.
-
IoT-Based Early Warning System: Install smart sensors for pressure and flow. Trigger alerts or automatic guide vane adjustments when:
-
Outlet pressure fluctuation > ±5%
-
Flow drops below 90% of Qjmin
-
4. Operational Best Practices – Eliminate Human Error
-
Standardized Start-Up/Shutdown Procedures:
-
Startup: Open anti-surge valve → then load the compressor.
-
Shutdown: Reduce load/pressure first → then close the valve.
-
-
Load Adjustment Guidelines: Limit step changes in load to ≤10% per adjustment to prevent instability.
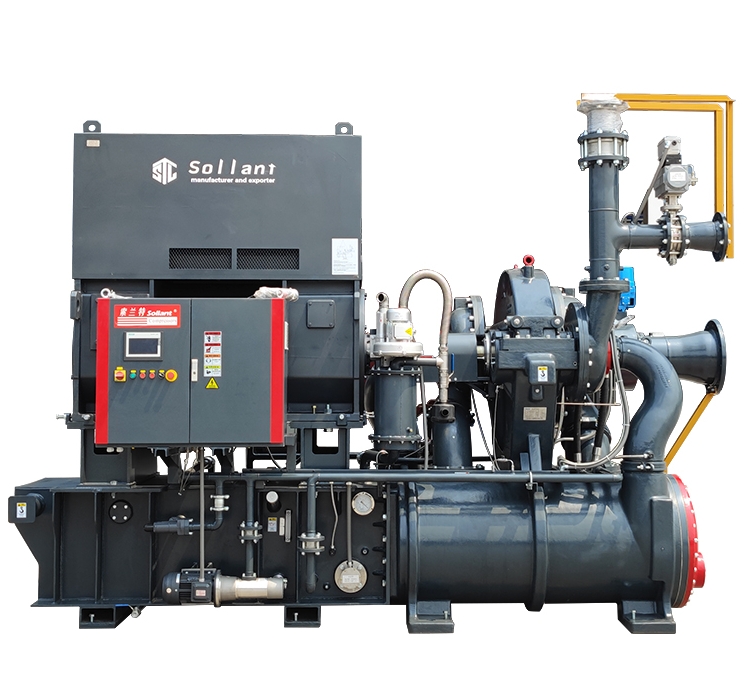
✅ Conclusion: Building a Surge-Resilient Compressor System
Surge prevention in centrifugal air compressors must be integrated across equipment design, maintenance practices, intelligent monitoring, and daily operation. With the right strategies in place, you can:
-
Extend compressor lifespan
-
Avoid costly downtime
-
Improve energy efficiency
-
Enhance plant safety
Looking for a tailored anti-surge solution or diagnostic support? Contact our technical experts or your compressor manufacturer’s support team for professional advice.