As a critical control component in an air compression system, the air compressor inverter regulates motor speed to adjust output pressure and flow. This enables energy savings and precise control. However, in real-world applications, various faults can arise, affecting the normal operation of the air compressor. This article explores seven common inverter faults, their causes, and effective solutions to ensure stable performance and longevity.
1. Inverter Overheating Fault
🔍 Fault Phenomenon:
The inverter overheats, causing an automatic shutdown for protection. In severe cases, prolonged overheating may result in permanent equipment damage.
🔎 Possible Causes:
- High Ambient Temperature: Poor ventilation or excessive room temperature leads to inefficient heat dissipation.
- Cooling System Malfunction: A damaged cooling fan or excessive dust accumulation on the heat sink affects cooling efficiency.
- Overloaded Operation: Running under excessive load for long periods generates excessive heat.
- Coolant Issues: Low coolant levels or clogged cooling pipes hinder heat dissipation.
✅ Solutions:
- Improve Ventilation: Ensure adequate airflow, install air conditioning if necessary, or add ventilation fans.
- Perform Regular Maintenance: Clean and inspect cooling fans and heat sinks periodically.
- Optimize Load Management: Avoid long-term overload and configure load parameters properly.
- Check the Cooling System: Regularly inspect coolant levels and clear any blockages in cooling pipes.
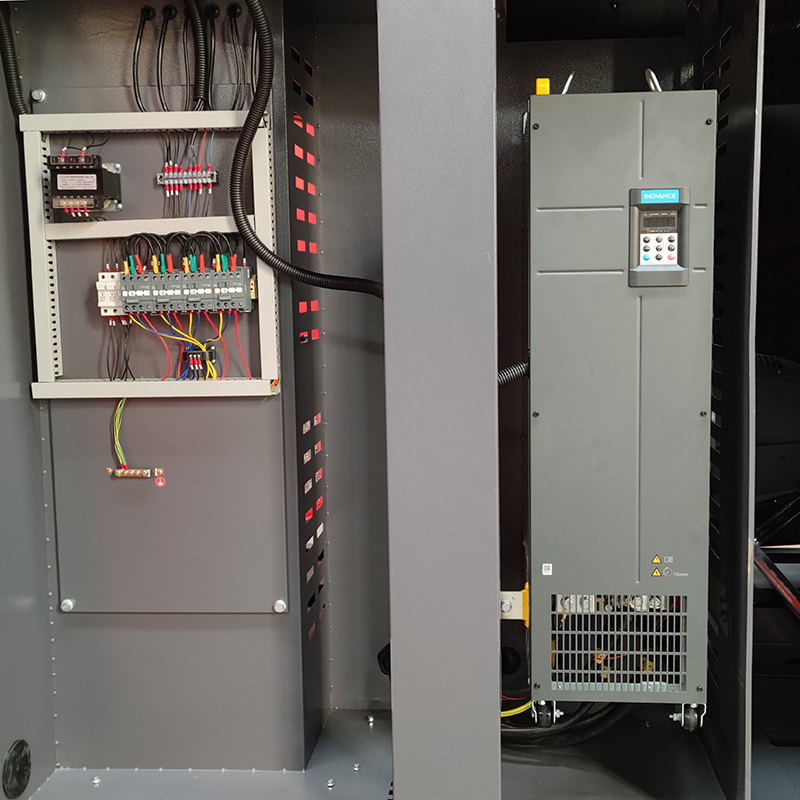
2. Inverter Overcurrent Fault
🔍 Fault Phenomenon:
The inverter detects excessive current during startup or operation, triggering an automatic shutdown.
🔎 Possible Causes:
- Sudden Load Increase: A rapid rise in load causes a sharp spike in motor current.
- Motor Issues: Short-circuited or grounded motor windings lead to abnormal current.
- Incorrect Parameter Settings: Unreasonably short acceleration times cause excessive starting current.
- Power Supply Fluctuations: Voltage instability leads to erratic current output.
✅ Solutions:
- Control Load Variations: Manage load changes smoothly to prevent abrupt spikes.
- Inspect Motor Condition: Regularly check motor windings and insulation for damage.
- Adjust Inverter Parameters: Optimize acceleration, deceleration, and overload protection settings.
- Stabilize the Power Supply: Use voltage stabilizers or UPS systems to maintain a consistent power supply.
3. Inverter Overvoltage Fault
🔍 Fault Phenomenon:
The inverter detects excessive voltage, leading to a shutdown for protection.
🔎 Possible Causes:
- Sudden Load Drop: A rapid decrease in load generates a back electromotive force (EMF), causing voltage spikes.
- Excessive Power Supply Voltage: Voltage exceeding the inverter’s rated capacity triggers overvoltage protection.
- Brake Resistor Malfunction: A damaged or incorrectly rated braking resistor fails to dissipate braking energy effectively.
- Incorrect Parameter Settings: Short deceleration times increase back EMF, leading to voltage spikes.
✅ Solutions:
- Stabilize Voltage Input: Install voltage stabilizers or use UPS systems.
- Check Braking Resistors: Regularly inspect and replace faulty resistors to ensure proper braking energy dissipation.
- Optimize Parameter Settings: Adjust deceleration times and configure overvoltage protection settings correctly.
4. Inverter Undervoltage Fault
🔍 Fault Phenomenon:
The inverter detects insufficient voltage, causing a shutdown to prevent operational instability.
🔎 Possible Causes:
- Low Power Supply Voltage: Voltage drops below the inverter’s minimum operating threshold.
- Faulty Power Lines: Poor connections or excessively long power cables cause voltage drops.
- Inverter Internal Malfunction: A damaged rectifier module or filter capacitor results in voltage instability.
✅ Solutions:
- Maintain Stable Voltage: Use voltage regulators or UPS systems to prevent undervoltage conditions.
- Inspect Power Lines: Ensure cables are in good condition, properly connected, and not excessively long.
- Repair or Replace Faulty Components: Identify and replace defective rectifier modules or capacitors as needed.
5. Inverter Communication Fault
🔍 Fault Phenomenon:
The inverter fails to communicate with the host computer or PLC (Programmable Logic Controller), leading to data transmission errors or system malfunctions.
🔎 Possible Causes:
- Communication Line Issues: Poor connections or damaged cables disrupt data transmission.
- Protocol Mismatch: Incompatibility between the inverter and PLC causes transmission errors.
- Internal Communication Module Failure: A malfunctioning inverter communication module leads to connectivity issues.
✅ Solutions:
- Check Communication Cables: Inspect and replace damaged cables while ensuring secure connections.
- Verify Protocol Compatibility: Confirm that communication settings between the inverter and PLC match.
- Repair or Replace Communication Modules: Address internal hardware failures promptly.
6. Inverter Grounding Fault
🔍 Fault Phenomenon:
The inverter detects an abnormal ground current, triggering a shutdown for safety.
🔎 Possible Causes:
- Motor Winding Insulation Failure: Damaged insulation causes an increase in leakage current.
- Inverter Internal Damage: Faulty internal components lead to improper grounding.
- Defective Power Line Grounding: Poor grounding in the power supply system results in erratic grounding currents.
✅ Solutions:
- Inspect Motor Insulation: Regularly check motor windings and insulation for damage.
- Repair Internal Inverter Components: Address any damaged parts affecting grounding.
- Ensure Proper Grounding: Check power supply grounding connections and correct any issues.
7. Inverter Module Failure
🔍 Fault Phenomenon:
The inverter fails to start or operate normally, with frequent protection shutdowns.
🔎 Possible Causes:
- Aging Components: Long-term use leads to wear and tear, reducing module performance.
- Overload Operation: Continuous excessive load causes internal module damage.
- Unstable Power Supply: Voltage fluctuations contribute to premature module failure.
✅ Solutions:
- Schedule Regular Maintenance: Periodically inspect and replace aging components.
- Optimize Load Management: Prevent long-term overload conditions by setting reasonable parameters.
- Stabilize Power Supply: Utilize voltage stabilizers or UPS systems to minimize fluctuations.
Conclusion
Air compressor inverters are prone to various faults related to temperature, load, power supply, communication, and grounding. By understanding these common issues and their causes, businesses can implement preventive measures to ensure smooth operation.
🔹 Key Takeaways:
✔️ Regular maintenance and inspections help detect and resolve issues early.
✔️ Optimized parameter settings enhance performance and prevent unexpected failures.
✔️ Stable power supply management minimizes risks associated with voltage fluctuations.
✔️ Effective cooling and ventilation prevent overheating and component degradation.
By following these best practices, companies can prolong the lifespan of their air compressor inverters, reduce downtime, and improve overall system reliability.
Sollant Signs Agreement with Spanish Distributor to Expand into the European Market!